La volta scorsa ho affrontato il calcolo di un indicatore tanto semplice quanto importante: il takt time. Un indice che mostra la quantità di prodotto finito che l’azienda deve produrre per mantenersi in linea con la richiesta del mercato. Il passo successivo riguarda l’utilizzo fattivo di questo indice, utile abbinato al grafico di yamazumi, per isolare eventuali colli di bottiglia (e non solo) e cercare le possibili soluzioni ad essi.
Il grafico vede sull’asse delle ascisse il tempo e su quello delle ordinate le fasi lavorative con i rispettivi tempi (immagine sotto)
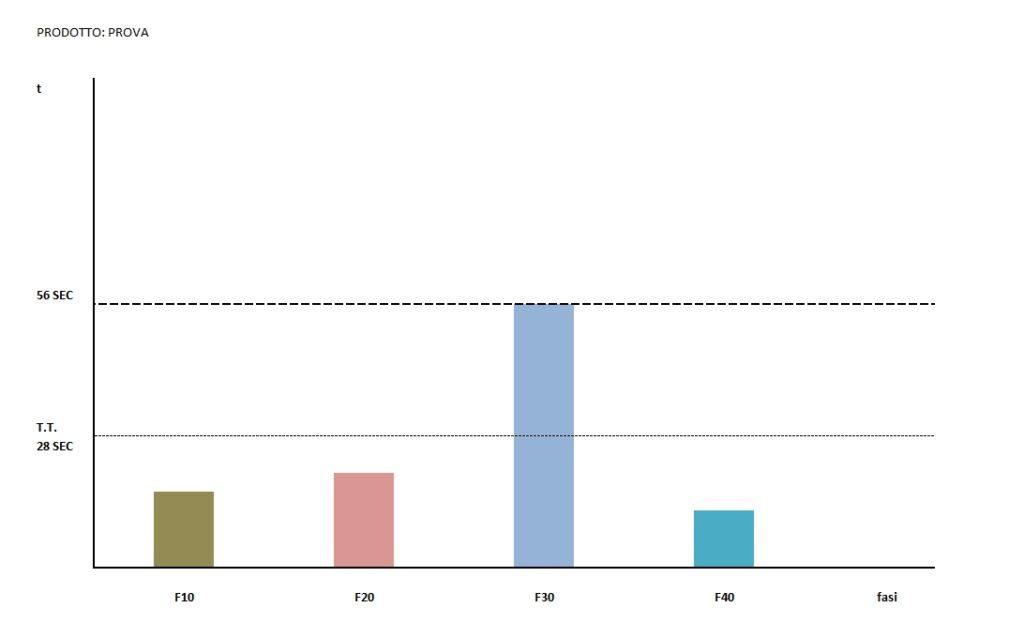
Le fasi rappresentate 10,20 e 40 presentano dei tempi al di sotto del takt time a sua volta pari a 28 secondi. Nessun problema quindi per queste 3 fasi, in quanto le operazioni ad esse riferite vengono appunto svolte in un tempo sufficiente affinché l’azienda possa “pulsare” al ritmo del mercato. I problemi nascono quando i tempi annessi alle fasi lavorative superano il t.t.. Nell’esempio di cui sopra, è evidente come la fase 30 duri il doppio del takt time, cioè 56 secondi. Ciò si traduce nella possibilità di realizzare un pezzo ogni 56 secondi e non certamente ogni 28 come vorrebbe il mercato. Un vero e proprio collo di bottiglia che comporta la riduzione della produzione alla metà di quanto richiesto dal mercato (appunto perché i tempi sono doppi).
In questi casi la prima domanda da porsi è: il tempo della fase 30 è un tempo uomo o un tempo macchina? Bene, perché se trattasi di tempo uomo, c’è da capire da cosa quei 56 secondi sono composti. Probabilmente nel lasso temporale preso ad oggetto sono presenti degli sprechi di tempo. Questi sprechi vanno individuati e eliminati, così da portare il tempo ad esempio a 40 secondi.
Questi 40 secondi a loro volta come si compongono? Sono riconducibili tutti ad un’unica fase oppure ci sono più operazioni elementari che li caratterizzano? Nella seconda ipotesi è ipotizzabile (qualora possibile) distribuire alcune di esse a monte (fase 20) o a valle (fase 40) così da poter abbassare il tempo della fase 40 sotto il t.t.. Nel caso invece in cui ci fosse una sola operazione che dura 40 secondi come ci si comporta? Beh, in questo caso non è che ci siano molte strade. Una di esse riguarda la duplicazione del centro di lavoro (es. fase 31) in modo da far si che ogni 40 secondi si abbiano 2 pezzi e non uno solo (quindi un pezzo ogni 20 secondi, quindi ben al di sotto del t.t.).
Qualora invece, tornando al quesito iniziale, il tempo di 56 secondi fosse tutto tempo macchina, come ci si comporterebbe? Bene, le opzioni sono queste:
– Duplicazione del macchinario se economica così da creare una fase 31
– Al costo di un buffer di semilavorato in accumulo a monte della fase 30, lasciar andare la produzione delle fasi 10 e 20 e poi, la fase 40, farla lavorare su due turni (se possibile), così da smaltire la produzione in eccesso
– Esternalizzare parte della produzione
– Rinunciare all’ordinativo in quanto non si ha al momento la capacità produttiva installata necessaria per sopperire alla domanda del mercato
Ogni caso chiaramente andrebbe analizzato a parte e le soluzioni possono essere spesso ibride fra loro. Certamente ciò che è assolutamente necessario è capire come, se per anticipare la crisi sia sufficiente l’analisi di bilancio, per garantire la continuità aziendale sia necessario agire lì dove la ricchezza si crea, cioè a dire in produzione. La funzione reale del controller è certamente questa. Noi ci rendiamo disponibili verso i professionisti tramite una nuova frontiera della formazione, per saperne di più clicca qui.