Nell’articolo precedente ho trattato di una serie di semplici accorgimenti volti all’ottimizzazione di tutte quelle attività a “non valore aggiunto” che possono essere ridotte a favore invece di attività a “valore aggiunto” (chi vuole trova gli articoli precedenti su questo blog oppure sul gruppo fb “controllo di gestione commercialisti e consulenti”). Le dispersioni, quando sono macroscopiche, saltano all’occhio in modo molto evidente. Questa è proprio la situazione che si è verificata presso l’impresa olearia oggetto della nostra case history: il repentino boom di vendite ha creato delle condizioni di squilibrio produttivo tanto significative quanto evidenti e, con una certa facilità, sono state prese delle contromisure idonee a riportare un buon livello di economicità lungo il flusso produttivo. Come anticipato quindi, quando “l’erba è alta” non ci sono grandi difficoltà ad effettuare una buona rasatura; il problema sorge quando l’erba è già ben tagliata e recuperare ore o addirittura minuti produttivi preziosi risulta essere un’impresa un po’ più delicata.
Prima di scendere nel dettaglio credo sia giusto spiegarmi meglio in merito al titolo di questo semplice trattato. Un articolo pubblicato qualche tempo fa titolava “il primo vero passo del commercialista” ed era incentrato alla definizione di una prima semplice mappatura, tramite rilevazione tempistica, dei cicli produttivi. Un successivo secondo articolo titolava “il secondo passo del commercialista” e trattava di un ulteriore interessamento del professionista in seno a decisioni legate all’ottimizzazione del flusso produttivo. Entrambi gli articoli mostravano come fosse semplice e proficuo, per il professionista, interessarsi anche delle dinamiche produttive in quanto legate a filo doppio all’andamento economico (e direi anche finanziario) di qualsiasi azienda di qualsivoglia dimensione dedita alla produzione di beni (ma altresì all’erogazione di servizi).
Questo terzo articolo invece scende un filino più nel dettaglio e mette in evidenza come, con un po’ di pratica ed oserei dire con un po’ di “spirito d’osservazione”, il commercialista può senza difficoltà alcuna davvero arrivare a fare la differenza, a vantaggio dell’impresa seguita e a vantaggio di sé stesso, nelle vesti di consulente aziendale richiesto dal mercato e differente dai propri colleghi, che magari un po’ si “cullano” nell’implementare un sistema di programmazione e controllo analizzando solo i dati di bilancio e/o comunque i dati provenienti esclusivamente dalla contabilità generale.
Fatta questa debita premessa riprendo alla svelta il taglio assolutamente operativo dei miei semplici articoli. La volta scorsa ci siamo lasciati con il quarto punto in sospeso: “l’ottimizzazione delle micro fermate”. Le micro fermate non si ottimizzano a “tavolino” come le macro fermate trattate nell’ultimo articolo, ma necessitano di una sorta di “osservazione” sul campo. Nel dettaglio prendo a riferimento una serie di interruzioni lungo la linea dovuta ad un piccolo collo di bottiglia e che non poche grane ha comportato agli operatori addetti.
Il caporeparto evidenzia come l’ultima macchina in linea, cioè la cartonatrice, porti 50 battute al minuto a fronte di 65 battute al minuto legate alle altre macchine della linea (quindi la cartonatrice risulta un po’ più lenta delle altre macchine poste in linea). Il caporeparto sostiene inoltre che i tecnici, dopo il collaudo, abbiano garantito come tutta la linea fosse correttamente bilanciata, ma nella realtà non ha riscontrato questo corretto bilanciamento.
Il lento accumularsi di bottiglie a valle, porta la linea a bloccarsi 4 volte ogni ora, in quanto la fotocellula di sicurezza posta un po’ più a monte rileva l’accumulo delle bottiglie in attesa e blocca la linea. Il caporeparto ha pensato di apportare una miglioria spostando la fotocellula il più a monte possibile e facendo si che l’accumulo si distribuisse non più su 3 metri ma su 6 metri di nastro. La figura sotto spiega il prima (a sinistra) ed il dopo (a destra).
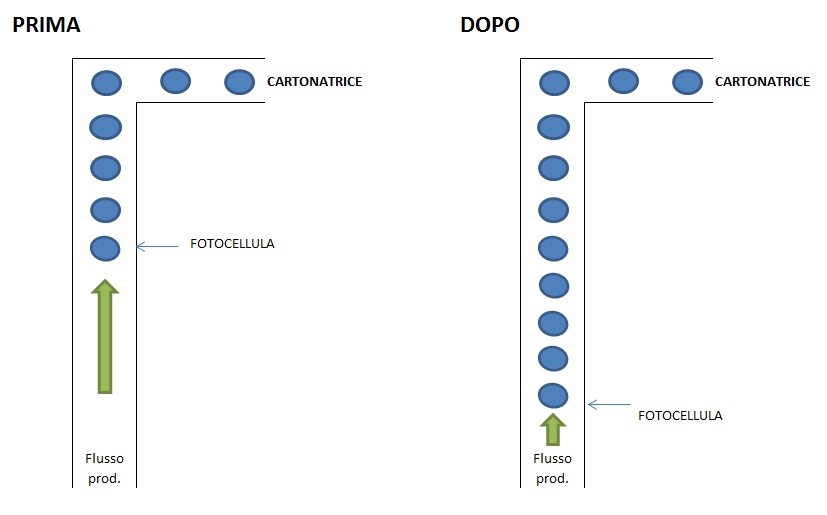
La foto reale riportata sotto rende meglio l’azione lean posta in essere dal solerte caporeparto e che ha portato la linea a bloccarsi non più 4 volte ogni ora ma “solo” 2 volte ogni ora (avendo raddoppiato il “serbatoio intermedio” di accumulo bottiglie)
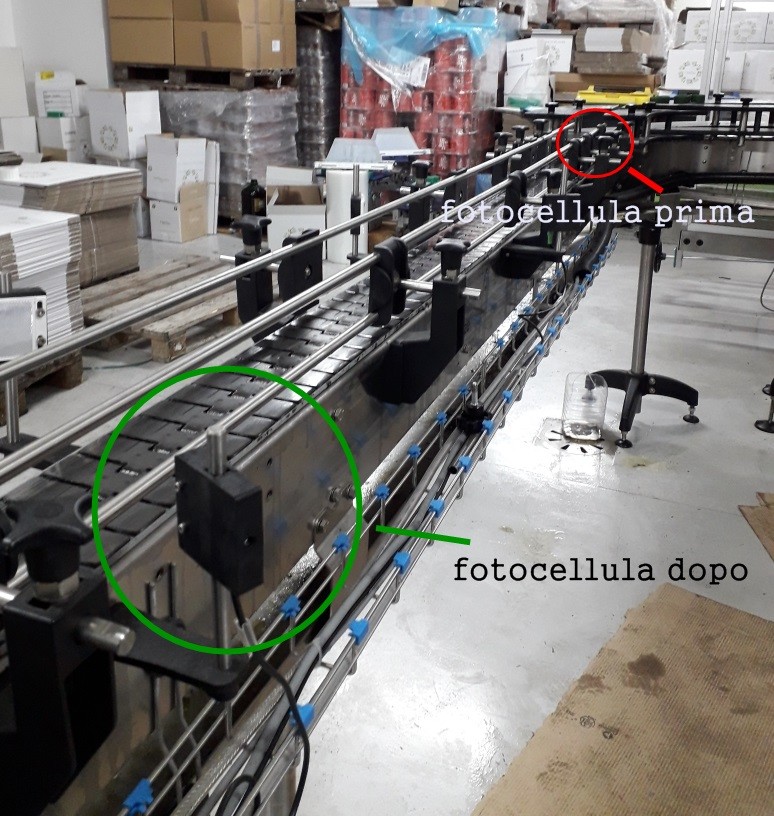
Partiamo dal presupposto che nella logica lean il parere degli operai (giustamente) è tenuto in debita considerazione (ed aggiungerei guai se non fosse così). La domanda che però mi sorge spontanea è:
“La miglioria posta in essere dal caporeparto è davvero stata corretta?”
Parrebbe di si, d’altronde le interruzioni si sono dimezzate e non è poca roba, evidenziando un netto miglioramento…Vorrei rispondere però con un’ulteriore domanda:
“In fondo è così difficile fare le cose semplici?”
Per chi ha avuto la pazienza di seguire i miei articoli ricorderà come il Cicle Time (tempo ciclo che segna l’andamento del ritmo produttivo) è dettato dalla macchina (o fase lavorativa) più lenta di tutta la linea. Il corretto bilanciamento della linea può eliminare i punti di accumulo indesiderati garantendo la continuità della produzione….che fare quindi? Basta semplicemente rallentare le macchine a monte della cartonatrice regolandole a 50 pz/min (stesso tempo di battuta della cartonatrice visto in precedenza) ottenendo il giusto bilanciamento dell’intera linea (tutte le macchine “viaggiano” alla stessa velocità), evitando l’accumulo finale e portando le interruzioni da 4 a Z E R O!
L’uovo di colombo vero?
Eppure nessuno aveva provato a cambiare punto di vista permettendo al caporeparto di ragionare ed eliminare del tutto quella fastidiosa fermata.
Vediamo ora, eliminato quell’inopportuno collo di bottiglia, cosa è successo nel costo di trasformazione di un prodotto preso a caso (screen shot seguente)
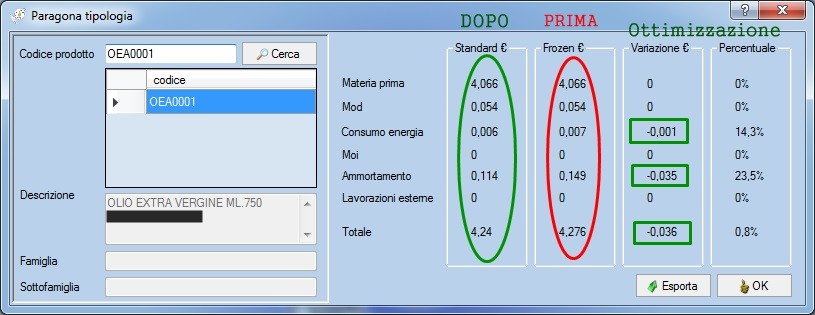
Si è partiti da un costo di trasformazione di 4,276 €, per passare ad un costo di 4,24 €, con un recupero pari a 3,6 centesimi…niente male per un azienda che opera in un settore ove si “combatte” sul filo del centesimo! Diamo quindi risalto ad una miglioria in un’azienda che presenta elevata meccanizzazione nei processi…figuriamoci su piccole realtà che lavorano su commessa e per reparti cosa ne può venire fuori!
In definitiva ci vuole solo un po’ di pratica unita ad un pizzico di buona volontà, nulla più e si può arrivare a fare la differenza di cui ho ampiamente trattato, soprattutto rispetto alla neo nata riforma della crisi d’impresa. In merito a questo epocale cambiamento, semplici diagnosi sullo stato di salute dell’azienda seguita serviranno davvero a poco, perché i vostri clienti vi chiederanno certamente le SOLUZIONI da adottare per “rientrare” dal potenziale sconfinamento degli alert…e queste soluzioni a parere di chi scrive dovranno essere prese in fretta, se si vuole evitare il tritacarne che il legislatore ha preparato per i “non meritevoli”. 18 mesi passano veloci, è bene partire con largo anticipo e cominciare perlomeno a rilevare i tempi di produzione e realizzare le distinte base, altrimenti come anticipato il rischio che si corre è fornire una diagnosi, per poi non essere pronti ad indicare la (certamente più importante) CURA!
Scopri le nuove date del nostro corso in “Controllo di Gestione e Crisi d’Impresa”. Per maggiori info, programma e prenotazioni clicca qui.