Con questo semplice articolo apro una miniserie di tre articoli inerenti i costi legati alle dispersioni lungo la linea produttiva (altri articoli simili sono presenti su questo blog sui gruppi fb/lk “controllo di gestione commercialisti e consulenti”). Le dispersioni in oggetto sono tra le piaghe più grandi che possano affliggere un imprenditore. Subdole, onnipresenti, spesso virali e quasi sempre accettate passivamente da chi dovrebbe combatterle con ogni mezzo (oramai epica l’affermazione in azienda: “Abbiamo sempre fatto così”). Oggi introduciamo qualche concetto che verrà meglio sviscerato nei prossimi capitoli.
Prima di iniziare, è giusto fare una debita premessa. Il commercialista che vuole diventare realmente controller (mio articolo precedente: “controllo di gestione: il primo VERO passo del commercialista), deve sapere che non sempre l’ausilio dell’imprenditore è pienamente trasparente. Alle volte capita che l’impresario costringa il proprio consulente ad una o più “cacce al tesoro”. La spiegazione può ricercarsi in alcuni casi in una certa diffidenza verso il proprio consulente, nel tentativo di “metterlo alla prova”; in altri casi celare la verità è un po’ come nascondersi dietro un dito e non voler ammettere, al consulente prima che a sè stessi, le proprie responsabilità. Fatta questa premessa, passiamo ai contenuti veri e propri.
Ve lo ricordate il nostro caro imprenditore oleario?… spero di si e, qualora così non fosse, trovate tutti gli articoli della case history ad esso associata sul mio profilo linkedin. A partire dal mese di luglio il nostro imprenditore ha inserito in organico un direttore commerciale che ha decuplicato la vendita dei prodotti portando nel giro di due mesi a saturazione l’importante linea produttiva. Innanzitutto devo ammettere come il mio scetticismo abbia perso nei confronti del fiuto dell’imprenditore (mai avrei immaginato una saturazione dell’impianto in così breve tempo ed in un mercato così maturo) ma mi riservo di capire con quali margini il direttore in questione ha intenzione di operare…è lì che si gioca la partita!
Venendo al dunque, è stato possibile effettuare un primo vero ribaltamento sul mese di ottobre 2018 (per “vero” intendo con l’impianto a pieno regime tutti i giorni), cioè un primo incrocio dei dati scaturenti dalla contabilità industriale (distinte base) rispetto i dati scaturenti dal profitti e perdite. In particolare voglio porre l’attenzione sul costo della manodopera. Sul profitti e perdite abbiamo il costo seguente
Manodopera diretta 2.800 € circa
Pari al costo di un operaio pienamente dedicato alla linea più due altri operai dedicati per 4 e 2 ore al giorno (ed assunti con sgravi contributivi)
Vediamo nel merito qual è “l’opinione” del software di co.in. bussolastar
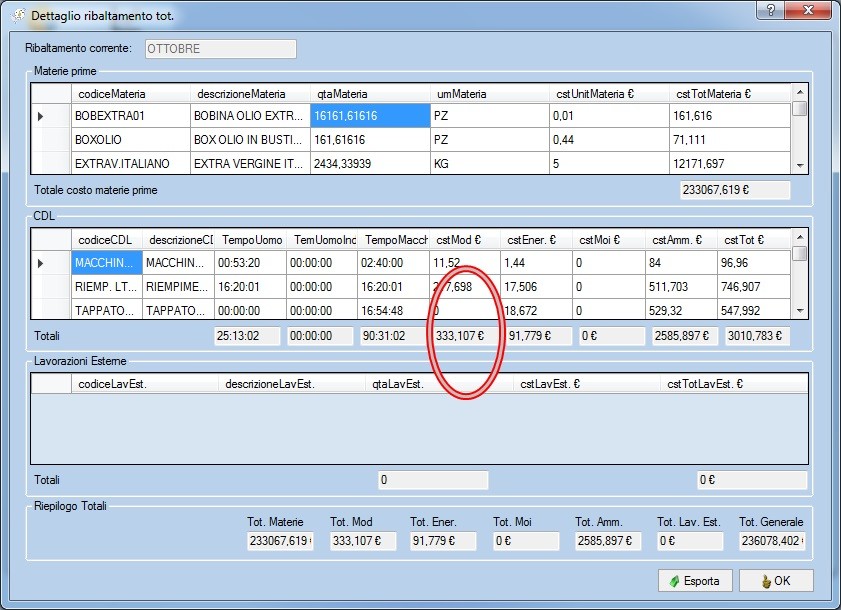
Il software ci indica, in funzione di tutta la produzione realizzata nel mese di ottobre e in funzione di quelli che sono i tempi standard caricati per i prodotti venduti, un costo standard pari a
333 € circa
La differenza fra i due valori, seppur in termini assoluti è quasi ininfluente, in termini percentuali è invece una voragine. Cosa è successo?
La risposta è semplice. Calcolando il totale di litri lavorati nel mese salta fuori un valore pari a 100.000. Dividendo 100.000 per il totale ore lavorate nel mese (8 ore per 22 giorni lavorativi), viene fuori un valore pari a circa 570 litri lavorati ad ora. Seppur grossolano come dato è, in questa fase iniziale, utile a chiarire alcuni aspetti.
In fase di attribuzione tempi, l’imprenditore ed il suo operaio scelto hanno giurato su questi livelli di output (prendo due codici prodotto per semplicità)
Olio lt 1 in vetro = 1.800 bottiglie ad ora = 1.800 lt/h
Olio lt 5 in latta = 1.300 latte ad ora= 6.500 lt/h
Performance in termini di output davvero abbondanti e completamente non corrispondenti al momento alla realtà. Invero la linea può anche toccare quei ritmi così elevati, ma quel ritmo riguarda ad esempio solo 10 o 12 minuti di produzione ogni ora, sottintendendo una velocità di punta toccata ma non mantenuta con la dovuta costanza. Ciò comporta un ritmo medio produttivo orario di gran lunga più contenuto.
Non va sottaciuto come molti prodotti abbiano inoltre subito in brevissimo tempo significativi cambiamenti, rendendo quasi immediatamente obsolete gran parte delle distinte definite la scorsa primavera. A ciò si è sommato l’incremento vertiginoso delle vendite che nel giro di brevissimo ha trasformato un ritmo produttivo piuttosto pacato, in una vera e propria rincorsa alla consegna, con tutti i problemi che ne sono conseguiti. Verificare e/o correggere i tempi ciclo in queste condizioni può risultare del tutto inutile. Bisogna quindi attendere che tutto si stabilizzi, a garanzia della dovuta costanza e continuità della linea produttiva.
Tornando al calcolo, risulta evidente quanto siamo distanti da queste due pseudo performance nel momento in cui i litri ad ora lavorati mediamente siano stati 570!
La giustificazione sembrerebbe risieda nel fatto che la linea è soggetta a continui fermi macchina (soprattutto setup). Quest’aspetto dovrà essere verificato (argomento dei due prossimi articoli, che consiglio vivamente di non perdere) in quanto le dispersioni a parere di chi scrive sono davvero troppo elevate. Le distinte base dovranno quindi essere tutte modificate (come detto poc’anzi) in funzione dei reali output orari (che per semplicità sono calcolati al lordo del tempo stimato dei fermi macchina).
L’imprenditore ed il suo capo reparto però cos’hanno fatto? Hanno indicato quale ritmo produttivo standard la velocità di punta che il pc legato all’impianto forniva, senza curarsi che la media fosse ben altra cosa. Probabilmente erano coscienti che il dato non fosse corretto, ma per qualche strano meccanismo mentale citato poc’anzi, hanno ritenuto opportuno fornire questi output. Al controller, a prescindere, spetta il compito di verificare i dati e soprattutto la coerenza degli stessi ed è questo il lavoro che è stato eseguito. Si potrebbe inoltre obiettare che al controller spetta anche il compito di prendere i tempi, senza “crogiolarsi” su dati forniti dall’azienda ed è vero, ma la presenza del controller sulle linee ha un costo che spesso l’imprenditore cerca, come in questo caso, di bypassare con tutti i rischi che poi ne conseguono.
Proviamo ora ad immaginare se non ci fosse stato un sistema di contabilità industriale che avesse permesso la controprova rispetto i dati dell’imprenditore…i prezzi praticati nel mese di ottobre e che hanno generato questo scostamento sfavorevole, sarebbero stati reiterati nel tempo, con tutte le conseguenze del caso!
La riforma della crisi d’impresa prevede quale obbligo la gestione della precrisi. Queste semplici analisi sono alla base di una corretta gestione che permetta di garantire una rosea continuità aziendale. Se si continua ad ignorare l’intervento (semplice, assolutamente semplice) sulle linee produttive, con grande probabilità ogni azione volta a rettificare l’eventuale cattivo andamento dell’impresa seguita sarà a mio avviso del tutto vana!
Scopri le nuove date del nostro corso in “Controllo di Gestione e Crisi d’Impresa”. Per maggiori info, programma e prenotazioni clicca qui.